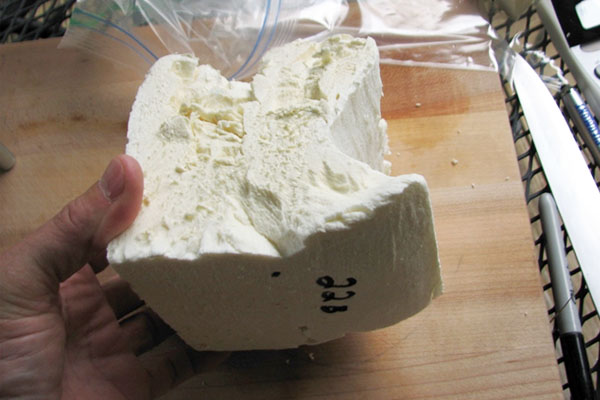
One example of foam shrinkage
Based on new blowing agent technology, many suppliers have recently developed new ccSPF formulations that allow the applicator to install foam in thicker lifts than before. This is welcome news for the industry in that applicators should be able perform more jobs efficiently with fewer excessive thickness lift issues such as excessive exothermic heat, odor, poor cell structure and poor dimensional stability.
Contrary to expectations; however, we have noticed a growing number of ccSPF contraction cases where the foam was installed within the supplier’s recommended lift thickness. This is where the foam shrinks from a stud creating a gap between the stud and the foam. This gap can prevent the SPF from performing effectively as an air barrier, reduces its insulation effectiveness and can create conditions that lead to condensation. While this gap may occur within a few hours, days or even weeks after installation, a callback for shrinkage problems after the drywall is installed can result in very expensive repairs.
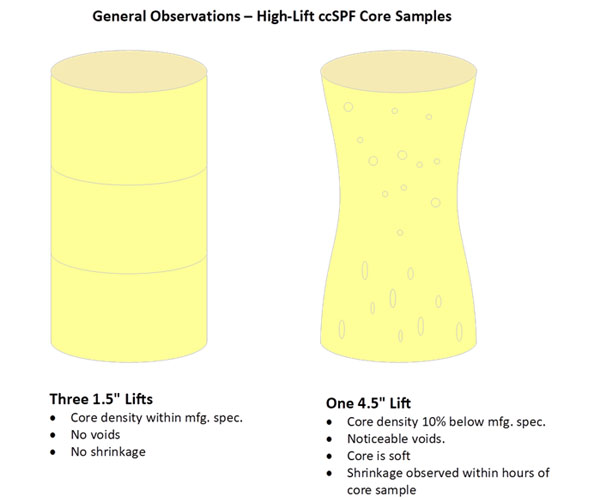
All foam plastics expand or contract to some degree. This expansion and contraction are referred to as dimensional stability. It is important to have the correct dimensional stability for the application. For example, a ccSPF that works well in a cold storage application may not perform as a roofing product.
SPFA in its technical guidelines and educational courses lists different types of ccSPF recommended for various applications. These types of ccSPF are identified in ASTM C 1029; Standard Specification for Spray Applied Rigid Cellular Polyurethane Thermal Insulation based primarily on compressive strength and dimensional stability.
Foam Type | Compressive Strength (minimum) | Dimensional Stability (percent linear change) |
---|---|---|
Type I | 15 psi | 12% |
Type II | 25 psi | 8% |
Type III | 40 psi | 6% |
Type IV | 60 psi | 4% |
The lower the percentage, the more stable the foam
ASTM D 2126; Standard Test Method for Response of Rigid Cellular Plastics to Thermal and Humid Aging is used determine the dimensional stability of foam plastics. It measures the dimensional changes of a sample when exposed to high heat and humidity. In most cases the foam sample expands, although it can shrink. The resulting change in length, width and thickness in a linear direction is recorded, and the maximum value in any direction reported as percent linear change.
In the case of ccSPF, samples are sprayed to a 2-foot square of plywood to a minimum thickness of 2 inches installed in 2 to 3 passes. A 12-inch square of foam is cut from the center of the plywood/foam specimen and the top of the foam is cut so the foam height is 1 inch and has one knit line in the foam. The sample is then placed in a humid aging chamber at 158⁰ F and 97% humidity. The linear percent change in length and width is reported at 24 hours and at 168 hours.
In previous years, SPF suppliers most often recommended a maximum lift thickness of 2 inches or less. The sample preparation in ASTM C1029 was based on maximum lift of 2 inches thickness. Now, many suppliers have foams with recommended lift thickness greatly exceeding 2 inches, one even recommends up to 8 inches.
When foam is installed in thicker lifts, the density and the compressive strength changes. The foam in the center of the sample is not quite as strong. It typically is less dense and exhibits a lower compressive strength. If the supplier is using the current ASTM C1029 sample preparation method, they may not have a good idea what the dimensional stability of the foam is at a thicker lift. Consequently, when checking out a foam’s physical properties, contractors should investigate dimensional stability on their own, using different pass thicknesses.
How to Identify ccSPF that is Likely to Contract
Test the foam yourself:
Before using a new foam, spray some samples onto a board or cardboard at different lift thickness, starting at 1 inch, then continuing up to the manufacturer’s maximum recommended lift thickness. Using a digital meat thermometer, measure the maximum interior temperature of the foam at the mid-thickness of the lift during cure and the time it takes to reach maximum temperature before the temperature starts to drop. If the maximum foam temperature is 200⁰F or under, it should be all right. (Somewhere between 200⁰F and 220⁰F is the maximum temperature for most foams before they exhibit excessive exothermic heat (blowholes, soft foam in the middle, discoloration, odor and poor dimensional stability). When the temperature of the foam begins to drop, more foam can be installed over the first lift.
After these samples have cured, use a coring tool to cut specimens from each sample. Allow these cylindrical specimens sit for 24 and 168 hours (one day and one week) at room temperature and observe the shape. Also, consider spraying assembly mockups before using high pass thicknesses in the field.
Obtain quality control samples before and during application:
Check out the middle of the foam core for discolored foam, elongated cells, cracks and fissures. Use the *thumb test or a field compression tester* to determine the compressive strength of the foam both perpendicular and parallel to rise. If it is softer in the middle than at the top and bottom, there is a good chance that foam could shrink.
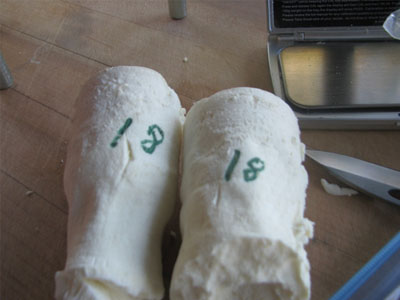
This closed cell SPF sample shrunk severely within one day after extraction. The foam was installed in lift thickness exceeding 4 inches and was very soft (less than 10 psi) in the lower center of the lift.
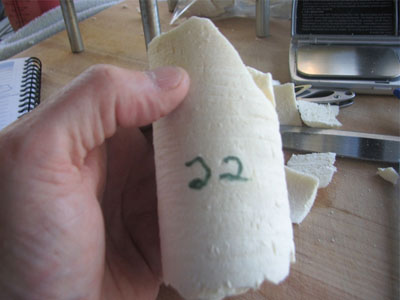
This sample was obtained from the same job but was sprayed in 1 to 1.5 inches thick lifts. It exhibited good compressive strength and dimensional stability.
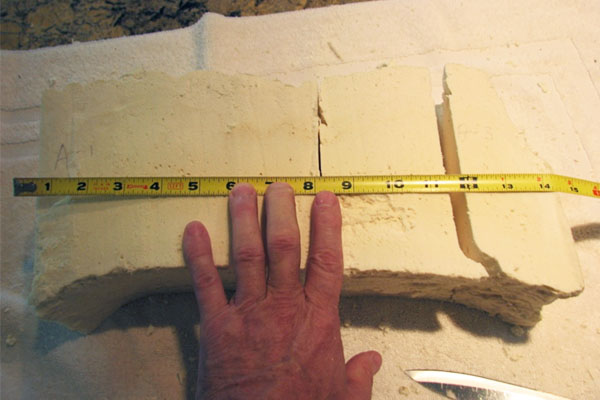
This is another example of closed cell foam that was sprayed too thick and contracted from the substrate.
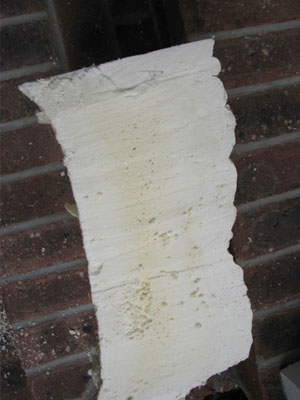
Note the darker foam in the center of the sample, indicating excessive exothermic heat developed during the initial cure.
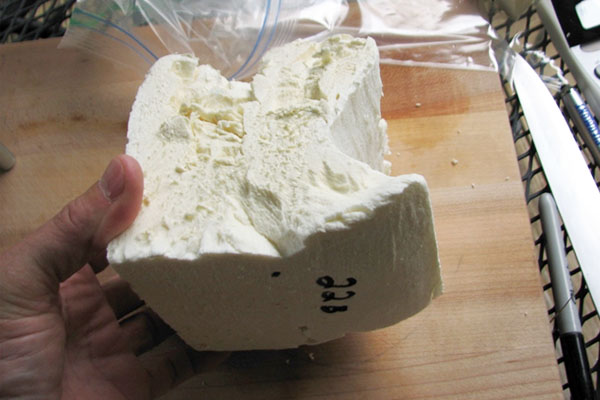
This horseshoe shaped contraction curve is common with closed cell SPF that has been sprayed in excessive lift thickness as it pulls away from a stud. The middle of the foam exhibited low compressive strength.
*Thumb Test:
An experienced foam applicator or inspector can typically tell within 5 psi the compressive strength of the foam by using the thumb test. Obtain a core sample of foam from the substrate. Cut off the top and bottom 1/3 of the core. Apply firm pressure with the thumb to the top of the sample. If the foam depresses ¼ inch, then it is approximately 25 psi. If it depresses 1/8 or less, then it is greater than 40 psi. Perform the same test to the sides of the sample as well. It should have similar compressive strength. If it is much softer, then the foam is more likely to shrink or contract.
Field Compression Tester:
If the foam is suspected of inadequate compressive strength, a sample can be obtained and measured with a field compressive strength tester such as a Com-Ten tool. Typically, a 2-pcf (pounds per cubic foot) density ccSPF would exhibit between 20 to 30 psi. If the foam is softer or harder than this, it is an indication of an off-ratio or poor mix.
Case Study:
A contractor recently performed this self-test procedure in their facility for a foam that was showing shrinkage problems in the field. They reported that the specimens with multiple passes remain cylindrical with straight sides and measured core densities within manufacturer’s tolerance. The single pass specimen formed into an hour-glass shape with significant shrinkage of the diameter of the cylinder at mid-thickness. The core density of the high-lift sample was about 10% below that of the manufacturer’s minimum density. A thumb test also showed that the foam for the high-lift specimen was softer and weaker than that of the multi-pass specimen.
What’s Next?
As noted earlier, there are materials standards for ccSPF, such as ASTM C1029, ICC-ES AC377 and soon-to-be published ICC-110⁰F, which may need to be modified to specifically require manufacturers to report physical properties, such as dimensional stability, compressive strength and density for foam installed at the maximum allowable pass thickness. Changing these consensus standards can take several months or a few years. In the meantime, contractors should perform these tests and spray mock-up assemblies before using high-lift foams in actual projects. If there are problems, report your concerns to the foam supplier.
About the Author
Mason Knowles is the President of Mason Knowles Consulting LLC, a consulting company specializing in providing technical information, education and training for the SPF industry. He has more than 48 years of experience in the spray polyurethane industry as a consultant, contractor, material supplier/manufacturer, equipment manufacturer and trade association professional. Website: Masonknowles.com