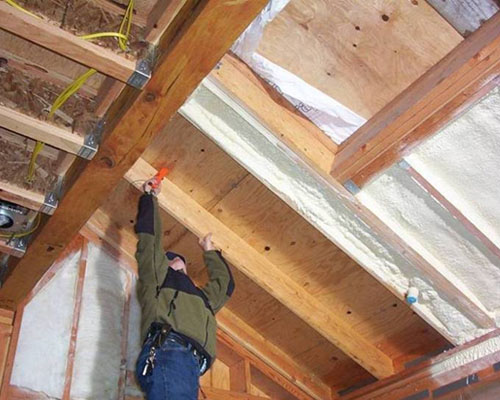
“Mason Knowles’ articles provide the benefits of attending a high-quality SPF training program--A must read for serious applicators.” Jay Davidson
SPF is a versatile material that can be a key component in addressing many building issues such as energy performance, air infiltration, moisture control, sound transmission, structural enhancement and more. However, even the best product won't work if the job is not done right.
As a consultant, I am frequently asked to inspect or evaluate an SPF application to determine if the product was installed correctly and/or to investigate a problem associated with the SPF.
What can go wrong?
- Poor adhesion
- Poor cell structure
- Poor dimensional stability (shrinking or cracking)
- Low density and compressive strength (2 pcf SPF)
- Strong odor and poor indoor air quality
- Poor moisture control
Most of these issues can be traced to errors in installation or off spec material. However, poor indoor air quality and moisture control can sometimes be traced to design issues.
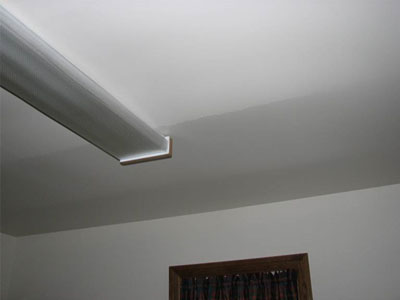
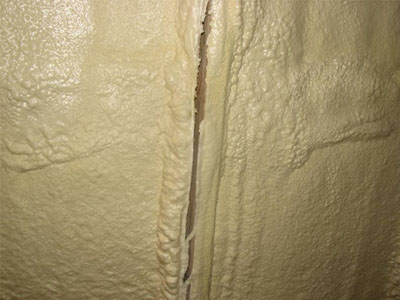
In this case the shrinking foam is bending and cracking the drywall
Application Quality Control
Substrate Preparation:
SPF can be installed to a variety of substrates including wood, concrete, metal, asphalt, foam sheathing, and others. But the substrate needs to be sufficiently clean and dry. Clean and dry means that it should be a surface that could be painted (wood moisture content less than 19%). If the surface is not sufficiently clean, the foam will not adhere well. If the surface is wet or damp, the A side of the SPF system reacts with the moisture instead of the B-side causing poor cell structure and adhesion. Substrate dryness can be measured with a moisture probe such as a Delmhorst Moisture Meter BD 2100.
Substrate Temperature:
SPF applications must be installed within the temperature and humidity levels recommended by the SPF manufacturer. While there is some variation among manufacturers, most SPF systems can be installed to substrate temperatures between 50 degrees F and 180 degrees F. (Note: Some suppliers have developed low temperature foams that can be installed to lower substrate temperatures.) SPF installed to cold substrate temperatures form high-density shellac like coating on the surface of the substrate that reduces the adhesive quality of the foam. In some cases, the foam can separate due to the difference in substrate temperature and the higher temperature of the rising foam.
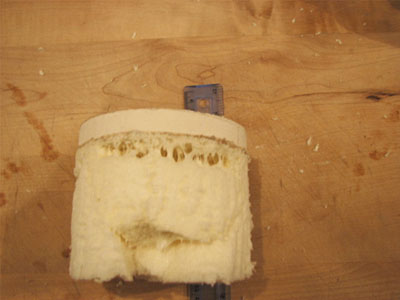
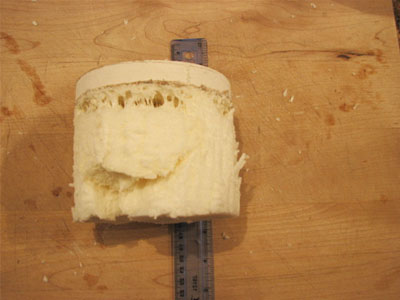
Low density SPF shows a large void and delamination near the substrate. The supplier attributes this problem to a cold substrate
Substrate Preparation--Common mistakes include:
- Failure to clean surface properly
- Applying SPF over moisture laden substrates
- Failure to identify acceptable substrates
How to Prevent:
- Substrate cleaning varies depending on the type of surface. Dusty surfaces typically can be wiped down. Some surfaces may require the use of solvents or cleansers to remove contaminants. In roofing applications, loose dirt and gravel can be removed with power brooms or vacuum. Some surfaces may require wet/vac equipment or power washing equipment to remove contaminants such as mud, grease, etc. (Note: follow SPF manufacturer's instructions for cleaning different substrates)
- Check substrate moisture content with a moisture meter, (such as a Delmhorst Contractor's Moisture Probe BD 2100). You can also use litmus paper to determine if the substrate is dry. If the paper turns color, the surface is too damp for application. If litmus paper is not available, spray a small test section (1’ x 1’) peel the foam while it is still pliable and check the foam substrate interface. If the foam has blowholes, poor cell structure, etc., it is too damp for application
- Visual inspections are a must to evaluate a substrate prior to application. Other methods of inspection or evaluation such as moisture surveys, adhesion/pull tests, core cuts, structural load analysis, etc. depends on the type of substrate
Humidity:
High humidity can introduce moisture into the liquid components of the rising foam. The foam cell structure can be affected leading to poor physical properties. The SPF industry recommends that foam applications not take place when the ambient temperature is within 5 degrees F of dew point.
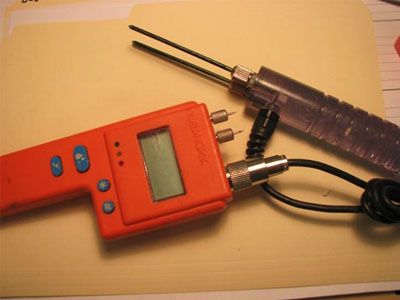
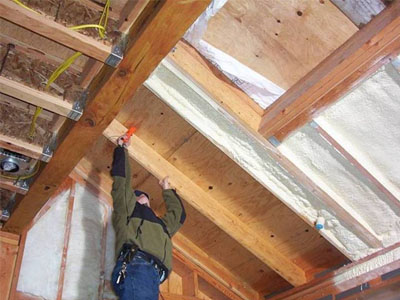
Delmhorst Moisture Probe can measure substrate humidity

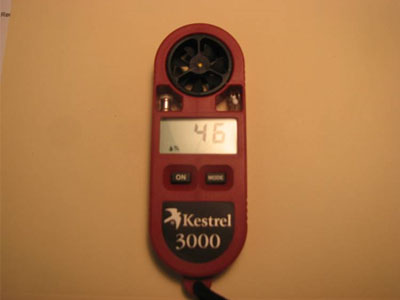
Temperature and humidity gauges tell the contractor if climate is adequate for sprayfoam application
Poor Mix:
Quality SPF requires the correct combination of heat, pressure and spraygun configuration (size of mixing chamber, mix module, nozzle or pattern control disc). SPF suppliers provide data sheets with instructions on the range of temperatures, pressures and spraygun configuration. Varying one or more of these elements can result in a poor mix of foam that can lead to problems.
Just like spray-painting and other applications that use pumps to install the product, the application of SPF systems is dependent on the sprayfoam equipment operating correctly. Sprayfoam equipment consists of two transfer pumps that send the liquid components to a proportioning pump. The proportioner heats and pressurizes the liquid to acceptable levels. Then the liquid components are sent in separate hoses to the spraygun. When the trigger is pulled at the spraygun, the material is mixed and sprayed onto the substrate. Each equipment component must operate efficiently for the foam to be installed correctly. If one transfer pump stops working, it can cause a crossover, filling the spraygun and sometimes the whip hose with reacted foam.
If the heaters do not work effectively the foam will not be hot enough to react properly. If the spraygun is dirty, the foam will not mix well.
Equipment Maintenance: Common problems and mistakes include:
- Failure to clean and maintain the spray gun.
- Drum pumps and ISO proportioner seizing up due to ISO (“A”) component buildup
- Contaminated hoses (usually the ISO or “A” component side)
How to Prevent:
- At the beginning of the day, never assume the spray gun is clean Material may have leaked into the gun overnight. Check the spray gun and pattern before spray application.
- If the spray pattern of the gun changes and cannot be adjusted correctly with heat or pressure, the spray gun probably requires cleaning. If cleaning the spray gun does not produce an acceptable pattern, gun parts such as mixing chambers, nozzles, impingers, etc. may need replacing.
- Clean spray gun thoroughly at the end of the day. (It should be as clean as the carburetor in your car)
Note: Some sprayfoam guns such as Graco’s Fusion gun do not require daily cleaning and should be cleaned when the pattern distorts and cannot be corrected with the cleanout drill
Improper Shipping and Storage of Liquid Components:
SPF systems have a shelf life of between 3 to 6 months depending on the system. This shelf life can be affected by temperature and humidity. Care should be taken by the supplier and contractor to ship and store materials properly. Materials stored in high temperatures can separate, losing their blowing agent to the air. Materials stored in cold environments can become so viscous that the liquid will not flow or mix properly. The A side can develop crystals causing material blockage and an off-ratio mix. Materials stored in the rain or very high humidity can develop condensation within the drum thereby contaminating the liquid component. Older materials can separate--absorb moisture, causing problems described above. In addition, over time the catalyst loses its effectiveness causing the reaction of the foam to be slow.
Materials: Common mistakes include:
- Failure to store materials (SPF or coating) at proper temperatures
- Not heating material to material manufacturer’s recommendations
- Allowing moisture contamination in opened drums
- Failure to use materials within the manufacturer’s recommended shelf life
How to Prevent:
- Maintain temperatures in storage facility within the manufacturers’ recommendation
- Allow 4 to 6 hours to heat cold materials before application
- Ensure partial drums of material are not exposed to high humidity. Cap drums overnight. Use dry air or nitrogen in partial drums to minimize moisture. Use partial drums first before opening new drums of material. Pour-up leftover material daily.
- Keep drum pumps submerged in material overnight
- Sink the ISO proportioner pump at the end of the day
- If contaminated material gets into the proportioner, flush the hoses as well as the proportioner using a material recommended by the SPF manufacturer. (Fresh material may be used to clean proportioner and hoses.) Begin spraying only when screens are clear of contaminated material.
Spray Technique:
The proper application of SPF requires different spray techniques for 2-pcf (pounds per cubic foot) SPF and 0.5-pcf SPF. Varying the spray technique can affect the overall quality of the foam application.
2lb SPF should be installed in lifts between 0.5 – 1.5 inches in depth (or as recommended by the supplier and confirmed by the applicator). The applicator should use a mixing chamber or nozzle of the right size so that the foam can be applied in passes that overlap 60% or more, making the foam grow at a uniform rate from one side to the other. When spraying between stud wall/ceiling cavities, the applicator should first picture frame the cavity. Let the foam set a few minutes then fill in the middle, spraying parallel to the direction of the studs. Each lift of foam needs to rest a sufficient time to allow exothermic heat created during the rise of the foam to dissipate.
Excessive exothermic heat can cause poor physical properties, cell distortion, high open cell content, discoloration or scorching of the foam and lingering odors. The contractor should check adhesion and cell structure and regular intervals throughout the day.
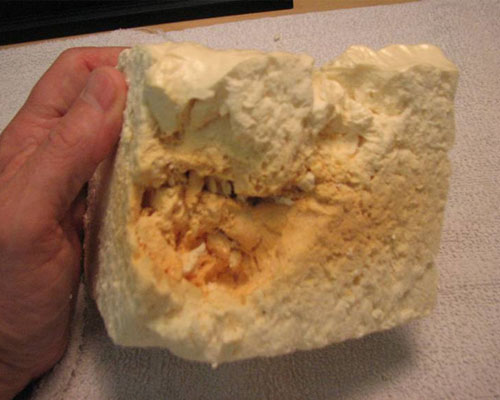
If the exothermic heat is high enough the foam
will scorch or in extreme cases catch on fire.
Note: See section below for procedures an applicator can use to determine how thick a lift can be installed).
Determining Lift Thickness of Closed Cell Foam
Before using a new foam, spray some samples onto a board or cardboard at different lift thickness, starting at 1 inch and then continuing up to the manufacture’s maximum recommended lift thickness. Using a digital meat thermometer, measure the maximum interior temperature at the mid-thickness of the foam during cure and the time it takes to reach maximum temperature before the temperature starts to drop. If the maximum foam temperature is 200F or under, it should be fine. (Somewhere between 200 and 220F is the maximum temperature for most foams before they exhibit excessive exothermic heat (blowholes, soft foam in the middle, discoloration, odor and poor dimensional stability). When the temperature of the foam begins to drop, then more foam can be installed over the first lift.
After the samples have cured, use a coring tool or saw to cut specimens from each sample. Allow the core samples to sit for 24 and 168 hours at room temperature. Observe the shape of the sample to see if it changes.
1/2 pcf SPF is typically installed in one lift to a stud wall or ceiling cavity to full thickness. The applicator should start at the bottom of the wall and work his way up. If there are hard to reach areas or spaces behind the studs, the applicator should picture frame those areas first to ensure against gaps and voids.
Design:
Sometimes the sprayfoam application is performed correctly but the foam was installed in wrong place, or the wrong thickness, or a vapor retarder was added that was not required, or one missing that was required. Make sure the design is suitable for its intended purpose. Nothing is worse than paying premium prices for a job that is doomed before it gets started. A few design mistakes include:
- Wrong material
- Improper thickness
- Vapor retarder issues
- Improper ventilation
- Wrong sizing of HVAC equipment
In order to minimize the design problems, each project should be evaluated based on the environment, climate (inside and out), HVAC equipment, use of the building, and anticipated occupant behavior. Hygrothermal modeling studies (such as WUFI or MOIST) can be conducted to determine thickness of insulation (and type) and where and what type of moisture control is required (vapor retarders, ventilation, etc.). For example, it would be a mistake to install a high water-vapor permeable material such as 0.5-pcf SPF in a crawl space where high humidity is a concern.
The designer and the HVAC contractor should understand and estimate the air sealing qualities of the foam in order to specify the correct type and size of HVAC equipment and ventilation package. In most cases, additional ventilation would be needed following a SPF application.
Manufacturer issues:
Issues related to the manufacturer are less frequent but include the following:
- Stored or shipped incorrectly
- Poor quality control during manufacturing
- Incorrect or misleading application information
Most manufacture issues are related to shipping and storage issues followed by incorrect application information. For example, a manufacturer recommends a closed cell SPF maximum lift thickness of 4 inches but exhibits problems at 3 to 4-inch lifts.
Poor quality off-spec foam from the manufacturer are relatively rare.
Masking and Trimming:
Sprayfoam can tenaciously stick to most surfaces and can drift fairly long distances from the point of application. A contractor should have an overspray plan for each job that includes masking or moving items in the immediate vicinity of the application that might get overspray.
Overspray: How to Prevent:
- Use windscreens on every exterior job.
- If something is close enough to the application area that overspray is a possibility, move it, mask it or cover it.
- When spraying an edge or small area, use a smaller pattern or tip and lower the pressure.
- In exterior applications, pay attention to wind direction as well as wind speed. If the wind changes direction, stop spraying and determine if a new overspray problem may exist. A 5 MPH wind blowing into a crowded parking lot causes much more damage than a 15 MPH wind blowing into an empty field.
- Assign a person to monitor overspray and direct parking.
- Post warning signs, tape off job site areas and notify personnel of spray schedule.
Odor and Exposure Control:
During application fumes and mists are created that are harmful to the health of the applicator and others in the installation area. Every contractor should have a safety plan specific to each job to prevent those fumes and mists from traveling to occupied areas and to prevent non-workers from entering the sprayfoam area during application. The industry standard is to contain, isolate and ventilate the spray area. Warning signs should be posted to designate the spray area and to prevent building occupants or other trades from entering the spray area.
Typically fumes and mist dissipate within a few hours to a few days depending on the amount of ventilation available, amount of foam sprayed, configuration of the area and the SPF formula. The contractor should determine how to ventilate the sprayfoam area and how long before occupants can re-enter the area. It should be noted that off spec foam could create odors that linger much longer than typical. The contractor should inspect the foam periodically to make sure the foam is not emitting odors beyond what is expected.
Application Tips:
- Don’t get greedy. If it’s too cold or too wet, do not spray.
- Pay attention to changing weather. Afternoon clouds could mean rain, higher humidity or dropping temperature.
- Be careful about spraying early in the morning or late in the evening except in warm and dry climates. Many contractors cause themselves problems by trying to start too early or spray too late.
Quality Control Inspection:
Once the sprayfoam application has been applied, how do you tell if it has been installed correctly?
The completed sprayfoam application should be inspected by a professional specifically trained on SPF building envelope applications. This can be a manufacturer’s representative, owner’s representative or 3rd party inspection company. A list of SPFA consultants is available at sprayfoam.org.
However, before a 3rd party inspection occurs, the SPF contractor should conduct their own quality control inspection during and immediately after the application.
Quality control sampling should be performed by the applicator within 15-20 minutes of the initial application and after the application is complete. Some of the items to look for include:
- Off-ratio or poorly mixed foam
- Thickness not meeting minimum average requirements or tolerances
- Foam separation from target or substrate
- Soft spots in the foam
- Hard spots in the foam
- Large color variations
- Foam density irregularities
- Compressive strength irregularities (thumb test)
- Wet, cold or contaminated surfaces
- Surface profile and texture
- Voids, gaps, cracks or fissures
- Adhesion
- Cell structure
- Overspray
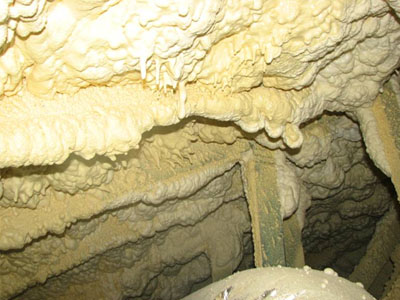
Very rough 2 lb. closed cell SPF application
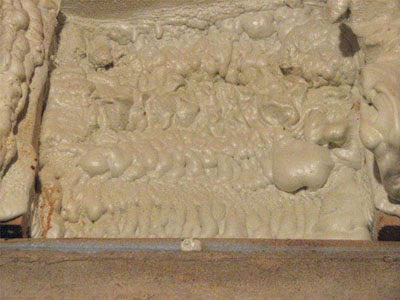
Color variations may indicate off-ratio or poorly mixed foam
SPFA inspection criteria require that the inspector measure and record a minimum of 15 points per assembly for the depth of the foam and report values for each measurement. The objective of this procedure is to determine if the contractor met the minimum thickness requirements in all points of the installation as well as evaluate the contractor’s ability to uniformly install the SPF onto the target in a manner to meet the minimum required thickness in all spots.
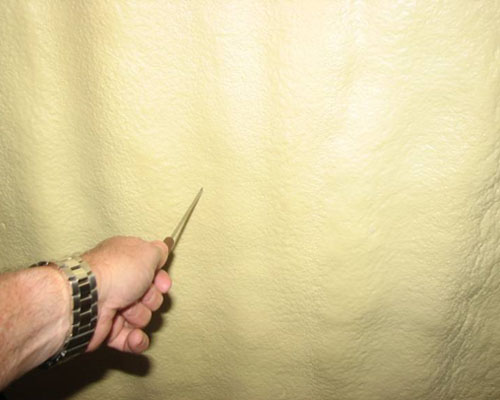
Measure depth of foam at the apparent lowest spot
So how does the inspector check for these anomalies?
Uniformity of sprayfoam application:
A good applicator can install closed cell foam within 1/4" tolerance at a 2 to 3-inch application in an open space. This means that the lowest point would be within 1/4 inch of the minimum specified thickness and no more than ¼” higher (making for a ½-inch total variation. In confined spaces, such as between stud wall cavities, the variation is typically greater due to a thicker application against the studs. For example, the interior of the wall or ceiling cavity range from 2.5-3.0 inches while the foam against the studs would vary from 3.0 to 3.5 inches in depth.
A good 0.5 pcf density SPF application would have a greater thickness variation due to the greater expansion rate of the foam. A ½-inch tolerance when spraying 3.5 to 5.5 inches of foam would be considered exceptional. Typically, 1/2 pcf foam would have a 3/4 inch to 1.0-inch tolerance between stud wall cavities.
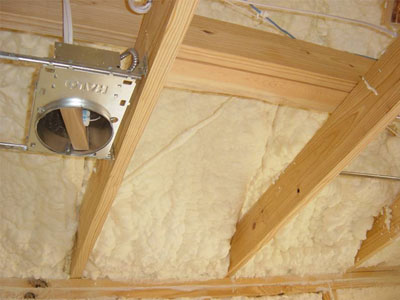
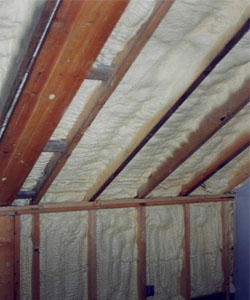
1/2 lb. SPF sprayed uniformly on walls and ceiling
Uniformity: SPF should be installed to a relatively uniform surface. Extreme variations of thickness and non-uniform applications can be a strong indication of other problems such as excessive lift thickness, high exothermic heat reaction and more.
Test compressive strength:
An experienced foam applicator or inspector can typically tell within 5 psi the compressive strength of the foam. If the foam is suspected of inadequate compressive strength, a sample can be obtained and measured with a field compressive strength tester such as a Com-Ten tool. Nominal 2-pcf density SPF ranges from 20 to 30 psi and low- density foam between 2-5 psi. If the foam is much softer or harder than this, it is an indication of an off-ratio or poor mix.
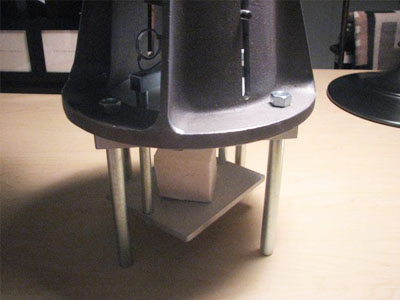
Testing for compressive strength with a Com-Ten

Coring tools or knives can be used to cut samples
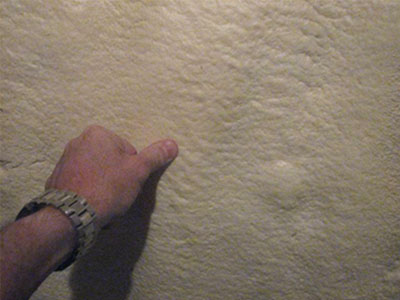
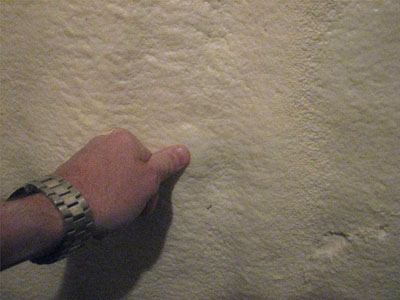
Adhesion and compressive strength can be estimated using the thumb test of 2 lb. SPF
Confirm adhesion:
An experienced foam applicator or inspector can typically tell within 5 psi the compressive strength of the foam. If the foam is suspected of inadequate compressive strength, a sample can be obtained and measured with a field compressive strength tester such as a Com-Ten tool. Nominal 2-pcf density SPF ranges from 20 to 30 psi and low- density foam between 2-5 psi. If the foam is much softer or harder than this, it is an indication of an off-ratio or poor mix.
Observation of the foam cell structure and quality.
Foam should have a consistent cell structure without significant color changes, cell deformation or other anomalies. Fissures, blowholes, dark or scorched area in the middle of the foam indicates high exothermic heat was developed within the foam during cure.
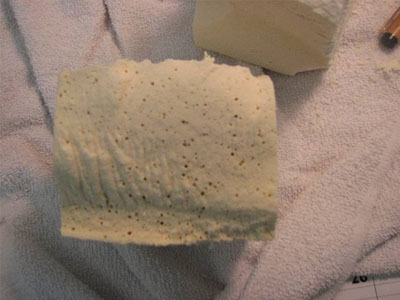
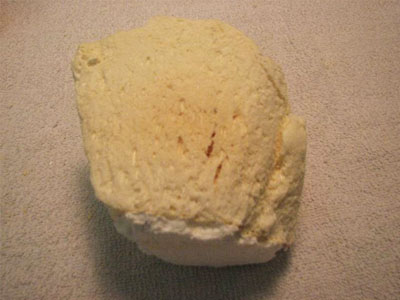
Excessive lift thickness & high exothermic heat can also cause blowholes and discoloration within the foam.
Repairs:
If poor foam quality is detected the foam should be removed and replaced. In most circumstances the following procedures would be performed:
- Identify off spec foam
- Remove with appropriate tools
- Treat substrate (if required) to enhance adhesion
- Closed Cell: Spray 0.5 to 1.0 thick passes until full thickness is achieved. (Allow exothermic heat to dissipate between lifts.)
- Open Cell: Install full thickness in one lift
It should be noted that thousands of SPF applications are installed each year with satisfactory results. It is important; however, for the consumer and the design team to understand the inspection process and how to recognize a quality foam application.
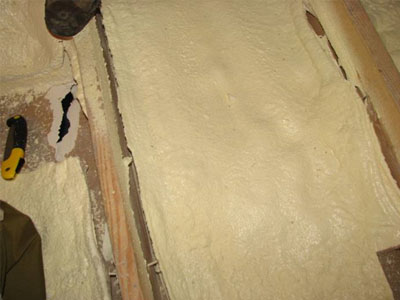
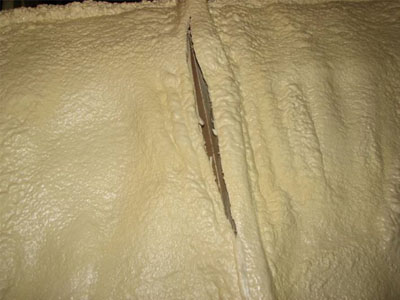
Shrinking foam can be caused by high exothermic heat, excessive lift thickness and a poor mix of materials.
The following 2 lb. SPF requires removal and replacement at the areas where it has shrunk back from the studs.
Mason Knowles is a member of Spray Polyurethane Foam Alliance (SPFA), Insulation Contractors Association of America (ICAA) and contributes frequent web-based presentations on SPF issues. He is a SPFA Certified Field Examiner, Chair of SPFA Consultant’s Committee, accredited building envelope and roofing inspector and instructor. Knowles chaired the ASTM committees on SPF roofing (D08.06) and standard specification for closed cell SPF (C-1029) for 20 years. He regularly writes articles for national trade journals, provides presentations for trade groups and other organizations on the SPF industry.
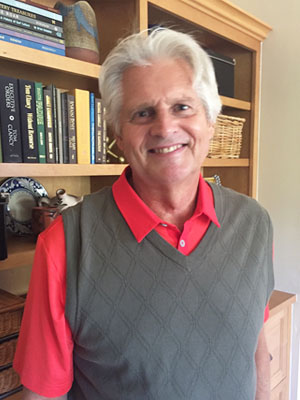
Knowles has more than 48 years of experience in the spray polyurethane industry as a consultant, contractor, material supplier/manufacturer, equipment manufacturer and trade association professional. For more information, contact 571-239-5221 or visit Masonknowles.com