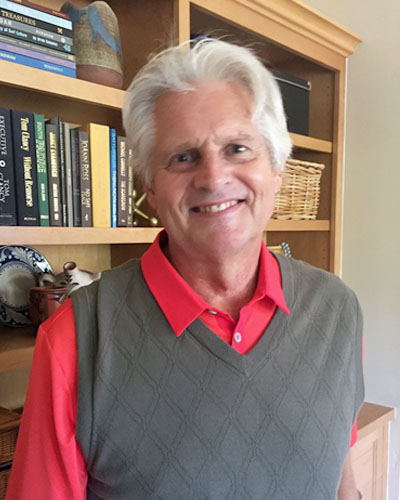
Mason Knowles shares his 48+ years
of experience in the SPF industry
Spray polyurethane foam (SPF) usage in residential applications has grown from less than 1% of all insulation used in the building envelope to well past 15% over the last 20 years. Builders, home owners and architects are discovering that it can be used to address many construction challenges, such as minimizing air leakage, providing reliable insulation, and along with proper ventilation, helping to control the interactions of heat, air and moisture within the building envelope.
During that time; however, several myths have been circulated within the construction industry about spray foam applications. Some of them have been advanced by members of our own spray foam community and adopted by competitive industries. A significant percentage of my work has involved addressing these myths.
In the many years I have worked in the spray foam industry, I have read mountains of building science articles, coordinated dozens of research projects, wrote numerous articles, made hundreds of presentations, visited more than a thousand job sites, and answered thousands of technical questions.
I have tried to be objective about my opinions and the facts, so the construction industry could make an informed decision on when, what, and where to use spray foam.
In this article, I would like to address a few of the claims that I would consider misleading, exaggerated or just plain false. As is often the case, there is a little bit of truth in each claim, so it becomes important to filter through negative marketing and true performance information. A few examples are:
- Closed-cell foam installed to the underside of wood roof decks will rot the deck because roof leaks go undetected due to the water resistance of the foam.
Closed-cell spray foam has been installed on the underside of wood roof decks for more than 50 years with great results. The historical record does not show that closed-cell SPF correctly installed to the underside of wood decking leads to deterioration from roof leaks. To the contrary, closed-cell foam is water resistant and will repel liquid water. It seals cracks and crevices in the wood deck so any water that gets past the roofing system stays on top of the wood deck and allows gravity to take it down to the edge of the building and off the roof. In colder climates, the SPF keeps the roof deck cold, so that ice damming is less likely to occur, further reducing the chance of water damage to the building.
- Closed-cell foam is a vapor retarder and cannot be used in warm, humid climates because it does not allow water vapor to go into and out of an assembly.
Closed-cell foam has a perm rating of approximately 1.5 per inch to 3 per inch and an R-value of approximately 6 – 6.8 per inch. This combination allows a controlled moisture vapor flow while separating the inside and outside temperature. The result is better control of condensation within the building envelope, so long as there is sufficient SPF insulation to prevent condensation. In most applications, 1 inch of SPF will suffice in warm and mixed climates and 2-3 inches in colder climates. (Note: hygrothermal modeling calculations are recommended when non-typical conditions occur such as extreme environments and unusual construction or design).
- Spray foam releases toxic gases, such as formaldehyde, after it cures. SPF off gassing contributes to poor indoor air quality.
SPF does not and never has had formaldehyde in its formulas. During application; however, fumes and mists are developed that can be harmful to health. Based on air monitoring data from decades of research, the most dangerous fumes and mists have dissipated within a few hours to 24 hours after applications. During application spray foam installers contain and ventilate the space during application and use respiratory equipment to protect themselves and others. Ventilation is continued after application for approximately 24 hours before re-occupancy.
SPF materials may give off a noticeable odor for several days after application. These odors are usually caused by unreacted amine catalysts, and have been described as smelling like fish, cat urine or fresh latex paint. They can be a general nuisance. Supplementary ventilation of the work area for a few days is recommended to reduce these odors. If other odors are present or persistent, or the foam is discolored or inherently sticky, or friable, these are symptoms of an improperly installed foam. In this event, contact the SPF contractor.
For the vast majority of the population these odors are obnoxious but not a health issue (similar to odors from cleaning fluid, paint or adhesives used in tile and granite installations). But, for chemically sensitive individuals, or folks that have chronic bronchial conditions, the odor may cause cold like symptoms and /or exacerbate their existing conditions. The most common solution for eliminating the odors is to remove the foam that was installed incorrectly. After a few days, the odor should diminish rapidly.
- Spray foam makes a building too tight.
Spray foam will make the building more airtight and that can affect the ventilation patterns. This is actually a positive because if the building is better air sealed, it is easier to condition the air going into and out of the space. Using tools such as blower door testing and HVAC calculations, we can design ventilation and HVAC equipment specifically for that building which will provide better indoor air quality than before. But, if the ventilation system is not designed properly, there can be a build up of VOCs within the building, which could lead to poorer indoor air quality.
- Spray Foam is almost impossible to install correctly and is likely to have issues due to the highly technical nature of the product.
There are specific industry best practices to follow in order to install SPF properly. Technical guidelines and industry sponsored educational courses developed over decades by industry professionals provide detailed information on the correct ways to install SPF that are relatively easy to follow. Quality control tools such as temperature/humidity/moisture meters enable the applicator to know when conditions are right to spray foam to a substrate. Spray foam contractors can use heaters, dehumidifiers, fans, etc. to condition interior spaces so that foam can be installed within the parameters recommended by the supplier.
Advances in spray foam equipment that includes digital, computerized control of pressure, temperature and ratio can also assist the applicator to install the foam within the manufacturer’s recommendation and industry best practices.
- Consumer complaints on spray foam applications are getting out of control and the industry has a big problem addressing them.
While we strive in the industry to eliminate all issues in the field, there are some legitimate consumer complaints that require action to correct. However, the actual number of consumer complaints that require remediation of the application is very small. Contrary to what you read on internet blogs, there are relatively few consumer complaints on spray foam applications compared to similar construction industries.
If you crunch the numbers, it is estimated that less than 1/10th of one percent of all spray foam jobs have a customer complaint that requires the contractor or supplier to remediate the application. * Of course, if you are the one with the issue, it doesn’t help that you are a distinct minority. Trade groups, suppliers and contractors are continually evaluating the causes of theses issues to provide remedies to reduce the total number.
* Averages are based on discussions with SPF manufacturers, contractors and consultants along with personal knowledge of specific consumer complaints compared to estimated total number of spray foam jobs annually.
In conclusion, look to authoritative sources for real information about SPF applications such as Spray Polyurethane Foam Alliance (SPFA), Spray Foam Coalition (SFC) Center for the Polyurethane Industry (CPI) Building Professionals Institute (BPI) and credible reports from government agencies such as EPA and OSHA. Ignore the noise of the internet blogs that tend to exaggerate, mislead, use inappropriate and inapplicable research and confuse the consumer.
Mason Knowles is the President of Mason Knowles Consulting LLC, a consulting company specializing in providing technical information, education and training for the SPF industry. For more information, contact Mason at Masonknowles.com